Budowa maszyn pneumatycznych opiera się na kilku kluczowych elementach, które są niezbędne do ich prawidłowego funkcjonowania. Wśród najważniejszych komponentów można wymienić sprężarki, które odpowiadają za wytwarzanie sprężonego powietrza. Sprężarka jest sercem systemu pneumatycznego, ponieważ to ona generuje ciśnienie, które napędza pozostałe elementy maszyny. Kolejnym istotnym elementem są siłowniki pneumatyczne, które przekształcają energię sprężonego powietrza na ruch mechaniczny. Siłowniki te mogą mieć różne kształty i rozmiary, w zależności od zastosowania, a ich wybór ma kluczowe znaczenie dla efektywności całego systemu. Również zawory pneumatyczne odgrywają ważną rolę w budowie maszyn pneumatycznych, ponieważ kontrolują przepływ powietrza w systemie. Dzięki nim możliwe jest precyzyjne sterowanie ruchem siłowników oraz innych komponentów. Nie można zapomnieć o przewodach i złączkach, które łączą wszystkie te elementy w jedną całość, umożliwiając swobodny przepływ sprężonego powietrza.
Jakie są zalety i wady maszyn pneumatycznych
Maszyny pneumatyczne mają wiele zalet, które sprawiają, że są popularnym wyborem w różnych branżach przemysłowych. Jedną z głównych korzyści jest ich prostota konstrukcji, co przekłada się na łatwość obsługi i konserwacji. Ponadto maszyny te charakteryzują się dużą szybkością działania oraz możliwością uzyskania dużej siły przy stosunkowo niewielkich rozmiarach. Dzięki temu są idealne do zastosowań wymagających precyzyjnego ruchu lub szybkiej reakcji na zmieniające się warunki pracy. Kolejną zaletą jest bezpieczeństwo użytkowania, ponieważ sprężone powietrze nie stwarza zagrożenia wybuchem ani pożarem, co czyni je bardziej bezpiecznymi niż maszyny elektryczne czy hydrauliczne. Niemniej jednak maszyny pneumatyczne mają również swoje wady. Ich efektywność może być ograniczona przez straty ciśnienia w systemie oraz konieczność regularnej konserwacji sprężarek i filtrów powietrza. Dodatkowo koszt zakupu niektórych komponentów może być wyższy niż w przypadku innych technologii, co może wpływać na decyzję o ich wyborze w danym przedsiębiorstwie.
Jakie zastosowania mają maszyny pneumatyczne w przemyśle
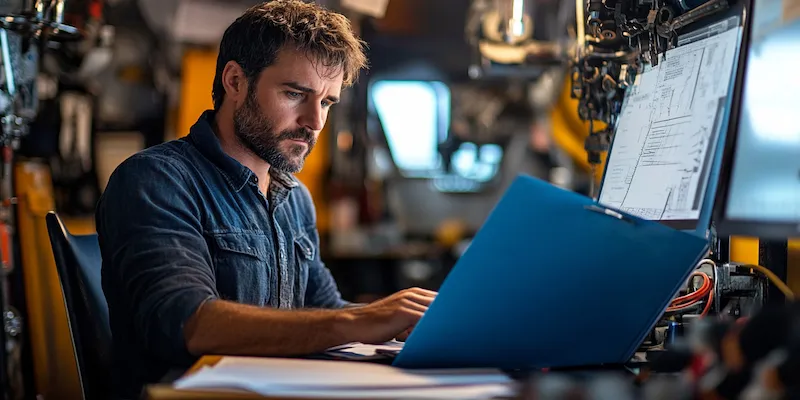
Maszyny pneumatyczne znajdują szerokie zastosowanie w różnych dziedzinach przemysłu, co czyni je niezwykle wszechstronnymi narzędziami. W branży produkcyjnej są często wykorzystywane do automatyzacji procesów montażowych oraz pakowania produktów. Dzięki swojej szybkości i precyzji siłowniki pneumatyczne mogą wykonywać skomplikowane ruchy, co znacznie zwiększa wydajność linii produkcyjnych. W przemyśle motoryzacyjnym maszyny pneumatyczne stosowane są do lakierowania oraz obróbki powierzchniowej części samochodowych, gdzie wymagane jest równomierne nanoszenie materiałów. Również w logistyce i magazynowaniu znajdują zastosowanie systemy pneumatyczne do transportu materiałów oraz manipulacji ciężkimi ładunkami. W branży spożywczej maszyny te są wykorzystywane do napełniania butelek oraz pakowania żywności, gdzie higiena i bezpieczeństwo są kluczowe. Dodatkowo w sektorze budowlanym maszyny pneumatyczne służą do zasilania narzędzi ręcznych oraz urządzeń do wiercenia czy cięcia materiałów budowlanych.
Jakie są nowoczesne technologie w budowie maszyn pneumatycznych
W ostatnich latach budowa maszyn pneumatycznych uległa znacznym zmianom dzięki postępowi technologicznemu. Nowoczesne technologie pozwalają na tworzenie bardziej zaawansowanych systemów pneumatycznych, które charakteryzują się większą efektywnością energetyczną oraz lepszą kontrolą nad procesami roboczymi. Przykładem innowacji są inteligentne zawory sterujące, które umożliwiają precyzyjne zarządzanie przepływem powietrza oraz automatyczne dostosowywanie parametrów pracy do aktualnych potrzeb produkcji. Dzięki zastosowaniu czujników i systemów monitorujących możliwe jest zbieranie danych o pracy maszyn, co pozwala na bieżąco analizować ich wydajność i identyfikować potencjalne problemy zanim staną się one poważnymi awariami. Wprowadzenie technologii IoT (Internet of Things) do budowy maszyn pneumatycznych otworzyło nowe możliwości związane z zdalnym zarządzaniem i diagnostyką urządzeń. Umożliwia to operatorom zdalny dostęp do informacji o stanie maszyn oraz ich parametrach pracy z dowolnego miejsca na świecie.
Jakie są kluczowe wyzwania w budowie maszyn pneumatycznych
Budowa maszyn pneumatycznych wiąże się z różnymi wyzwaniami, które mogą wpływać na ich wydajność oraz niezawodność. Jednym z głównych problemów jest zarządzanie ciśnieniem w systemie. Niewłaściwe ustawienia ciśnienia mogą prowadzić do nieefektywnego działania maszyn, a w skrajnych przypadkach nawet do ich uszkodzenia. Dlatego tak ważne jest, aby inżynierowie projektujący maszyny pneumatyczne dokładnie analizowali wymagania dotyczące ciśnienia i dobierali odpowiednie komponenty, które będą w stanie sprostać tym wymaganiom. Kolejnym wyzwaniem jest zapewnienie odpowiedniej jakości sprężonego powietrza. Zanieczyszczenia, takie jak wilgoć czy cząstki stałe, mogą negatywnie wpływać na działanie maszyn, prowadząc do ich szybszego zużycia oraz awarii. W związku z tym konieczne jest stosowanie filtrów oraz osuszaczy powietrza, co zwiększa koszty eksploatacji systemu. Dodatkowo, ze względu na dynamiczny rozwój technologii, inżynierowie muszą być na bieżąco z nowinkami i trendami w branży pneumatycznej, co wymaga ciągłego kształcenia i adaptacji do zmieniających się warunków rynkowych.
Jakie są najpopularniejsze zastosowania siłowników pneumatycznych
Siłowniki pneumatyczne to kluczowe elementy w budowie maszyn pneumatycznych i mają szerokie zastosowanie w różnych branżach przemysłowych. Jednym z najpopularniejszych zastosowań siłowników pneumatycznych jest automatyzacja procesów produkcyjnych, gdzie wykorzystywane są do podnoszenia, przesuwania i obracania elementów. Dzięki swojej szybkości i precyzji siłowniki te idealnie sprawdzają się w liniach montażowych, gdzie wymagane są szybkie cykle pracy oraz minimalizacja przestojów. W przemyśle motoryzacyjnym siłowniki pneumatyczne są często stosowane do obsługi narzędzi montażowych oraz urządzeń lakierniczych, gdzie ich zdolność do generowania dużych sił przy niewielkich rozmiarach jest niezwykle cenna. Również w branży spożywczej siłowniki te znajdują zastosowanie w procesach pakowania oraz napełniania produktów, gdzie precyzyjne sterowanie ruchem jest kluczowe dla zachowania wysokiej jakości produktów. W logistyce siłowniki pneumatyczne są wykorzystywane do manipulacji ciężkimi ładunkami oraz automatyzacji transportu wewnętrznego.
Jakie są różnice między technologią pneumatyczną a hydrauliczną
Wybór między technologią pneumatyczną a hydrauliczną często zależy od specyfiki zastosowania oraz wymagań dotyczących wydajności i bezpieczeństwa. Główna różnica między tymi dwiema technologiami polega na medium roboczym – w przypadku technologii pneumatycznej jest to sprężone powietrze, natomiast w hydraulice wykorzystuje się ciecz, najczęściej olej hydrauliczny. Technologia pneumatyczna ma wiele zalet, takich jak mniejsze ryzyko wycieków czy pożarów, co czyni ją bardziej bezpieczną w niektórych aplikacjach. Ponadto maszyny pneumatyczne są zazwyczaj lżejsze i bardziej kompaktowe niż hydrauliczne odpowiedniki, co ułatwia ich instalację i transport. Jednakże technologie hydrauliczne oferują większą moc i precyzję w porównaniu do systemów pneumatycznych, co czyni je bardziej odpowiednimi do zastosowań wymagających dużych sił lub precyzyjnego sterowania ruchem. W przypadku hydrauliki możliwe jest uzyskanie znacznie większych ciśnień roboczych niż w systemach pneumatycznych, co otwiera nowe możliwości zastosowań w przemyśle ciężkim czy budowlanym.
Jakie są trendy rozwoju technologii maszyn pneumatycznych
W ostatnich latach obserwuje się dynamiczny rozwój technologii maszyn pneumatycznych, który jest napędzany przez potrzeby rynku oraz innowacje technologiczne. Jednym z głównych trendów jest rosnące zainteresowanie efektywnością energetyczną systemów pneumatycznych. Producenci coraz częściej poszukują rozwiązań pozwalających na zmniejszenie zużycia energii poprzez optymalizację procesów oraz wdrażanie nowoczesnych komponentów o niższym oporze przepływu powietrza. Wprowadzenie inteligentnych systemów zarządzania pozwala na monitorowanie zużycia energii oraz dostosowywanie parametrów pracy maszyn do aktualnych potrzeb produkcji. Kolejnym istotnym trendem jest integracja technologii IoT (Internet of Things) z systemami pneumatycznymi, co umożliwia zdalne monitorowanie stanu maszyn oraz ich parametrów pracy. Dzięki temu operatorzy mogą szybko reagować na ewentualne problemy oraz optymalizować procesy produkcyjne na podstawie danych zbieranych w czasie rzeczywistym. Również rozwój materiałów kompozytowych i lekkich stopów metali przyczynia się do tworzenia bardziej zaawansowanych konstrukcji maszyn pneumatycznych, które charakteryzują się mniejszą wagą i większą odpornością na uszkodzenia mechaniczne.
Jakie są najczęstsze błędy przy projektowaniu maszyn pneumatycznych
Projektowanie maszyn pneumatycznych to skomplikowany proces, który wymaga uwzględnienia wielu czynników technicznych oraz operacyjnych. Niestety, podczas tego procesu często popełniane są błędy, które mogą prowadzić do obniżenia wydajności lub nawet awarii urządzeń. Jednym z najczęstszych błędów jest niewłaściwe dobranie komponentów do specyfiki danego zastosowania. Na przykład wybór siłownika o niewłaściwej sile może skutkować jego niedostateczną wydajnością lub przeciążeniem systemu. Kolejnym powszechnym problemem jest brak odpowiedniej analizy przepływu powietrza w systemie, co może prowadzić do strat ciśnienia i obniżenia efektywności pracy maszyny. Również zaniedbanie kwestii związanych z jakością sprężonego powietrza może prowadzić do szybszego zużycia komponentów oraz awarii systemu. Niezrozumienie zasad działania zaworów sterujących może skutkować nieprecyzyjnym działaniem całego układu pneumatykowego.
Jakie są przyszłościowe kierunki rozwoju maszyn pneumatycznych
Przyszłość maszyn pneumatycznych zapowiada się obiecująco dzięki ciągłemu postępowi technologicznemu oraz rosnącym wymaganiom rynku przemysłowego. Jednym z kluczowych kierunków rozwoju będzie dalsza automatyzacja procesów produkcyjnych z wykorzystaniem zaawansowanych systemów sterowania opartych na sztucznej inteligencji i uczeniu maszynowym. Takie rozwiązania pozwolą na jeszcze większą optymalizację pracy maszyn oraz lepsze dostosowanie ich parametrów do zmieniających się warunków produkcji. Również rozwój technologii bezprzewodowej komunikacji otworzy nowe możliwości związane z integracją różnych komponentów systemu pneumatycznego w jedną całość, co zwiększy elastyczność i efektywność procesów produkcyjnych.