Destylarka do rozpuszczalnika to urządzenie, które wykorzystuje proces destylacji do oddzielania substancji na podstawie ich temperatury wrzenia. W praktyce oznacza to, że destylarka podgrzewa mieszaninę, a następnie zbiera pary, które powstają w wyniku tego podgrzewania. Pary te są następnie schładzane i kondensowane z powrotem w cieczy, co pozwala na uzyskanie czystego rozpuszczalnika. Tego rodzaju urządzenia mają szerokie zastosowanie w przemyśle chemicznym, farmaceutycznym oraz w laboratoriach badawczych. Dzięki nim można efektywnie odzyskiwać rozpuszczalniki, co jest korzystne zarówno z ekonomicznego, jak i ekologicznego punktu widzenia. Warto również zauważyć, że destylarki mogą być wykorzystywane do produkcji różnych substancji chemicznych oraz w procesach oczyszczania. W zależności od konstrukcji destylarki, można uzyskać różne stopnie czystości końcowego produktu, co jest istotne w kontekście specyfikacji wymaganych przez różne branże.
Jakie są najczęstsze typy destylarek do rozpuszczalników
Na rynku dostępnych jest wiele różnych typów destylarek do rozpuszczalników, które różnią się zarówno konstrukcją, jak i przeznaczeniem. Jednym z najpopularniejszych rodzajów są destylarki prostokątne, które charakteryzują się prostą budową i łatwością w obsłudze. Są one idealne dla małych laboratoriów oraz dla osób prowadzących działalność hobbystyczną. Innym typem są destylarki kolumnowe, które umożliwiają bardziej zaawansowane procesy separacji dzięki zastosowaniu kolumny frakcyjnej. Tego rodzaju urządzenia są stosowane głównie w przemyśle chemicznym oraz farmaceutycznym, gdzie wymagana jest wysoka jakość końcowego produktu. Kolejnym interesującym rozwiązaniem są destylarki próżniowe, które działają w obniżonym ciśnieniu, co pozwala na destylację substancji o wysokiej temperaturze wrzenia bez ryzyka ich degradacji. Wybór odpowiedniego typu destylarki zależy od specyfiki procesu oraz wymagań dotyczących jakości uzyskiwanego rozpuszczalnika.
Jakie są kluczowe cechy dobrej destylarki do rozpuszczalnika
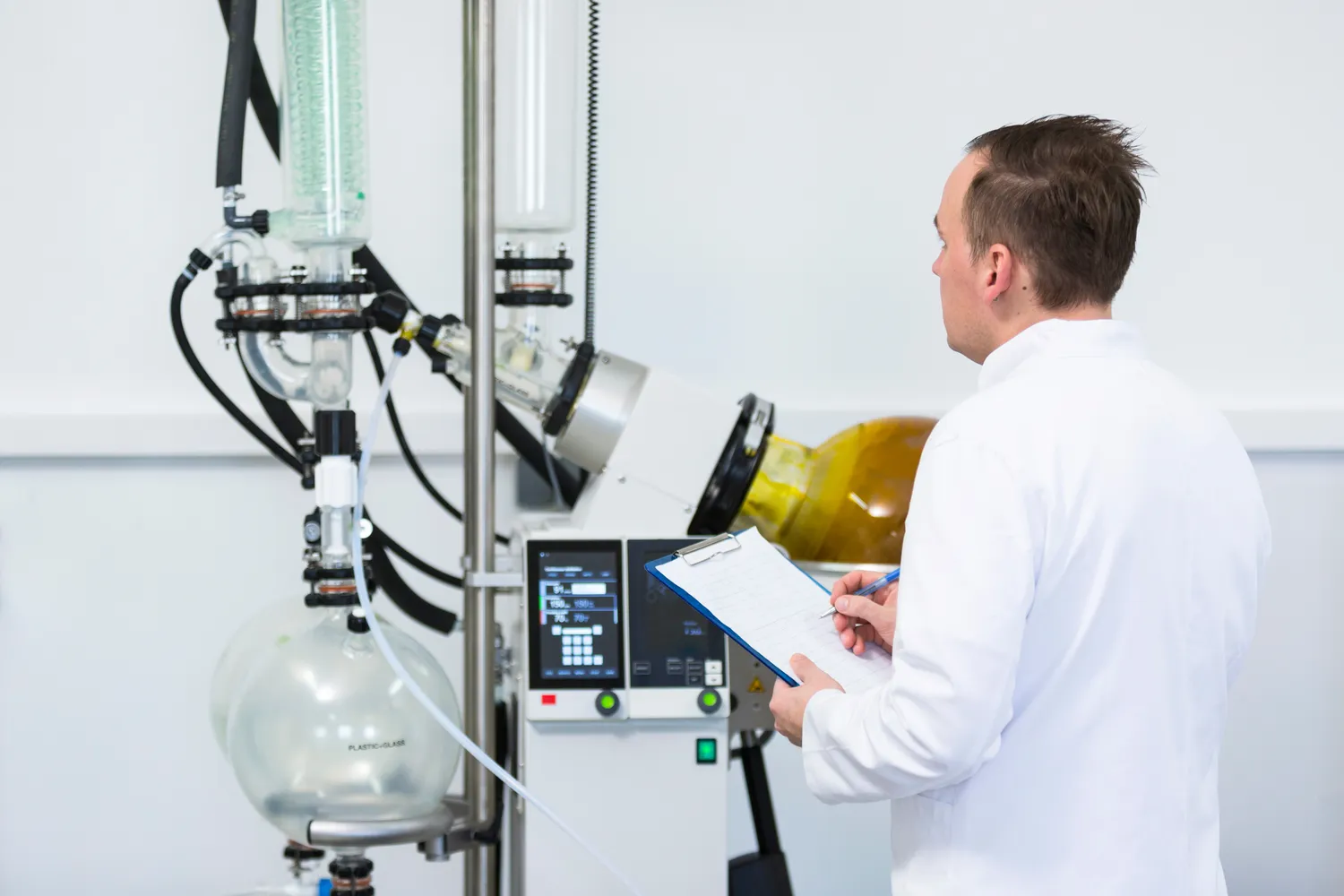
Kiedy planujemy zakup destylarki do rozpuszczalnika, warto zwrócić uwagę na kilka kluczowych cech, które mogą znacząco wpłynąć na jej wydajność i funkcjonalność. Przede wszystkim istotna jest pojemność urządzenia – im większa pojemność, tym więcej substancji możemy jednocześnie przetwarzać. Ważnym aspektem jest również materiał wykonania destylarki; najlepsze modele są zazwyczaj wykonane ze stali nierdzewnej lub szkła borokrzemowego, co zapewnia odporność na działanie agresywnych chemikaliów oraz wysoką temperaturę. Kolejną cechą wartą uwagi jest system chłodzenia; skuteczny system chłodzenia pozwala na szybsze kondensowanie par i zwiększa efektywność całego procesu. Dobrze zaprojektowana destylarka powinna także posiadać możliwość regulacji temperatury oraz ciśnienia, co daje większą kontrolę nad procesem destylacji. Ostatnim elementem jest łatwość w czyszczeniu i konserwacji; urządzenie powinno być zaprojektowane tak, aby umożliwić szybkie demontaż i dostęp do wszystkich jego części.
Jakie są koszty zakupu i eksploatacji destylarki do rozpuszczalnika
Koszty zakupu oraz eksploatacji destylarki do rozpuszczalnika mogą się znacznie różnić w zależności od wybranego modelu oraz jego funkcji. Na rynku dostępne są zarówno proste urządzenia dla amatorów, których ceny zaczynają się od kilkuset złotych, jak i profesjonalne modele przemysłowe kosztujące nawet kilkadziesiąt tysięcy złotych. Przy wyborze odpowiedniej destylarki warto uwzględnić nie tylko cenę zakupu, ale także koszty eksploatacyjne związane z jej użytkowaniem. Do takich kosztów należy zaliczyć zużycie energii elektrycznej potrzebnej do podgrzewania substancji oraz ewentualne koszty serwisowania czy wymiany części eksploatacyjnych. Warto również pamiętać o kosztach związanych z zakupem surowców do procesu destylacji oraz ewentualnymi kosztami związanymi z utylizacją odpadów chemicznych powstałych podczas pracy urządzenia. W przypadku profesjonalnych zastosowań istotne mogą być także koszty związane z przestrzenią roboczą oraz zapewnieniem odpowiednich warunków bezpieczeństwa dla pracowników obsługujących urządzenie.
Jakie są najważniejsze zasady bezpieczeństwa przy używaniu destylarki do rozpuszczalnika
Bezpieczeństwo podczas korzystania z destylarki do rozpuszczalnika jest kluczowym aspektem, który należy wziąć pod uwagę przed przystąpieniem do pracy. Przede wszystkim, użytkownik powinien być świadomy potencjalnych zagrożeń związanych z substancjami chemicznymi, które będą poddawane destylacji. Należy zawsze stosować odpowiednie środki ochrony osobistej, takie jak rękawice, gogle ochronne oraz fartuchy laboratoryjne, aby zminimalizować ryzyko kontaktu z niebezpiecznymi substancjami. Ważne jest także, aby prace związane z destylacją przeprowadzać w dobrze wentylowanym pomieszczeniu lub pod wyciągiem laboratoryjnym, co pozwoli na usunięcie szkodliwych oparów. Użytkownik powinien również zapoznać się z instrukcją obsługi urządzenia oraz zasadami jego prawidłowego użytkowania, aby uniknąć niebezpiecznych sytuacji. Kolejnym istotnym elementem jest regularne sprawdzanie stanu technicznego destylarki; wszelkie uszkodzenia lub nieszczelności mogą prowadzić do poważnych konsekwencji. Oprócz tego, warto mieć pod ręką odpowiednie środki gaśnicze w przypadku pożaru oraz znać procedury postępowania w sytuacjach awaryjnych.
Jakie są różnice między destylacją prostą a frakcyjną w kontekście rozpuszczalników
Destylacja to proces, który można przeprowadzać na różne sposoby, a dwa najczęściej stosowane to destylacja prosta i frakcyjna. Destylacja prosta polega na podgrzewaniu cieczy do momentu jej wrzenia, a następnie zbieraniu pary, która kondensuje się w chłodnicy. Ten sposób jest skuteczny w przypadku mieszanin składających się z dwóch substancji o znacznie różniących się temperaturach wrzenia. W praktyce oznacza to, że jeśli jedna substancja ma znacznie niższą temperaturę wrzenia niż druga, to destylacja prosta może być wystarczająca do ich oddzielenia. Z kolei destylacja frakcyjna jest bardziej zaawansowaną metodą, która wykorzystuje kolumnę frakcyjną do separacji składników mieszaniny na podstawie ich temperatur wrzenia. Dzięki temu możliwe jest uzyskanie większej czystości produktów końcowych oraz separacja substancji o podobnych temperaturach wrzenia. Destylacja frakcyjna jest szczególnie przydatna w przemyśle chemicznym i petrochemicznym, gdzie często zachodzi potrzeba oddzielania wielu składników jednocześnie.
Jakie są korzyści z używania destylarki do rozpuszczalnika w laboratoriach
Używanie destylarki do rozpuszczalnika w laboratoriach niesie ze sobą wiele korzyści, które wpływają na efektywność pracy oraz jakość uzyskiwanych wyników. Przede wszystkim, dzięki zastosowaniu tego urządzenia możliwe jest odzyskiwanie rozpuszczalników, co przekłada się na oszczędności finansowe oraz zmniejszenie ilości odpadów chemicznych. W laboratoriach badawczych często zachodzi potrzeba oczyszczania substancji chemicznych przed ich dalszymi analizami; destylarka umożliwia uzyskanie wysokiej czystości produktów, co jest kluczowe dla wiarygodności wyników badań. Dodatkowo, nowoczesne destylarki często wyposażone są w systemy automatyzacji, co pozwala na zwiększenie wydajności pracy oraz ograniczenie błędów ludzkich podczas procesu destylacji. Korzystanie z destylarki przyczynia się także do poprawy bezpieczeństwa pracy; dzięki możliwości odzyskiwania rozpuszczalników można ograniczyć ich ilość używaną w laboratorium oraz zmniejszyć ryzyko związane z ich przechowywaniem i utylizacją.
Jakie są najczęstsze problemy związane z eksploatacją destylarki do rozpuszczalnika
Podczas eksploatacji destylarki do rozpuszczalnika mogą wystąpić różnorodne problemy techniczne i operacyjne, które mogą wpłynąć na efektywność procesu destylacji oraz jakość uzyskiwanego produktu. Jednym z najczęstszych problemów jest niewłaściwe ustawienie temperatury; jeśli temperatura jest zbyt wysoka lub zbyt niska, może to prowadzić do niepełnej separacji składników lub degradacji substancji chemicznych. Innym problemem mogą być nieszczelności w układzie chłodzenia lub połączeniach, co może prowadzić do utraty pary i obniżenia wydajności urządzenia. Zdarza się również, że kolumna frakcyjna ulega zapchaniu przez osady lub inne zanieczyszczenia; regularne czyszczenie i konserwacja są kluczowe dla utrzymania sprawności urządzenia. Użytkownicy mogą także napotkać trudności związane z kontrolowaniem ciśnienia wewnętrznego; niewłaściwe ciśnienie może prowadzić do nieefektywnej pracy urządzenia oraz zwiększonego ryzyka awarii.
Jakie są najlepsze praktyki konserwacji destylarki do rozpuszczalnika
Aby zapewnić długotrwałą i efektywną pracę destylarki do rozpuszczalnika, konieczne jest przestrzeganie najlepszych praktyk konserwacyjnych. Regularne czyszczenie urządzenia jest kluczowe dla jego prawidłowego funkcjonowania; resztki substancji chemicznych mogą gromadzić się wewnątrz kolumny frakcyjnej czy chłodnicy i prowadzić do obniżenia wydajności procesu destylacji. Po każdym użyciu warto dokładnie przepłukać wszystkie elementy wodą demineralizowaną lub innym odpowiednim rozpuszczalnikiem neutralnym. Dodatkowo, należy regularnie sprawdzać stan uszczelek oraz połączeń; wszelkie nieszczelności mogą prowadzić do utraty pary oraz obniżenia efektywności pracy urządzenia. Warto także zwracać uwagę na stan elementów grzewczych; ich regularne czyszczenie pozwala uniknąć problemów związanych z przegrzewaniem czy uszkodzeniami mechanicznymi. Kolejnym istotnym aspektem konserwacji jest monitorowanie parametrów pracy urządzenia; wszelkie odchylenia od normy powinny być natychmiast analizowane i korygowane.
Jak wybrać odpowiednią destylarkę do rozpuszczalnika dla swoich potrzeb
Wybór odpowiedniej destylarki do rozpuszczalnika powinien być dokładnie przemyślany i dostosowany do indywidualnych potrzeb użytkownika oraz specyfiki wykonywanej pracy. Na początku warto określić swoje wymagania dotyczące pojemności urządzenia; jeśli planujemy przetwarzać duże ilości substancji chemicznych, lepiej zdecydować się na model o większej pojemności. Następnie należy zwrócić uwagę na rodzaj materiałów użytych do produkcji destylarki; modele wykonane ze stali nierdzewnej czy szkła borokrzemowego będą bardziej odporne na działanie agresywnych chemikaliów niż te wykonane z plastiku czy innych materiałów mniej odpornych na wysokie temperatury. Kolejnym krokiem jest analiza funkcji dodatkowych; nowoczesne modele często oferują zaawansowane systemy automatyzacji oraz monitorowania parametrów pracy, co może znacząco ułatwić obsługę urządzenia i zwiększyć jego wydajność.